
A place for all things Radio Controlled |
Come sign up on the new forum ----- www.myrcguide.com |
|
| Blue Ray 450se Upgrades & Tips | |
| | Author | Message |
---|
TRISTAR7737
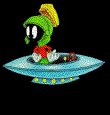
 | Subject: Blue Ray 450se Upgrades & Tips Tue May 12, 2009 7:53 pm | |
| This is a walkthrough for doing an upgrade for a BR 450se using the part # 18H-MM0029 When you open the packet – take note of the pitch extension ball parts (you want to use them). Use the supplied linkage parts if you need to replace your ball linkages ( I didn’t need to do that). The packet also contains replacement bolts and nuts for the main rotor and top of the drive shaft, and a bolt for connecting the drive shaft to the drive gear. Note that the shaft supplied is 108mm, the shaft your replacing is 115mm (keep your stock shaft if you can use it). If it is bent, a replacement shaft will be required. You can’t perform the upgrade with the supplied shaft, it is not long enough to reach your drive gear where you can secure it. If you have the 18H-MM0029 MEASURE IT, if it is 108mm, ask who you bought it from to send you the (18H-MM0047)shaft.What will you need:Tools: .5mm allen wrench drivers (preferably two for tightening frame bolts) Small needle nose pliers (for nuts on .5mm bolts) Very small Phillips driver (jeweler size) Ball linkage pliers (to remove or install swashplate linkages) Small rod or toothpick (to help with aligning shaft to drive gear) Supplies: Locktite (remove-able – blue) Containers to keep replacement parts separate from stock parts Preparation steps- Remove the main blades, and flybar and paddles
Caution – the stock plastic flybars thread into the flybar itself i. Tip – the carbon fiber upgraded paddles have allen bolts to tighten and adjust them onto the flybar. 1. I would recommend once you compete the head installation, once you re-install the flybar weights and get the flybar paddles where you want them, use a drop of CA glue to secure the plastic paddles to the flybar itself. Then put the weights back and secure them with the allen bolts. 2) Check the flybar to make sure it is straight, roll it on a flat surface (I didnt do this at first on my setup and I have a wobble I believe is due to the main shaft being slightly bent, so check yours first) 3) Be ready for small parts – the nuts used for the allen bolts for the CNC head, and your stock head are very small, as is the screw for your swash plate ball and pitch extension. So have a work area were these will not get lost easily.
- Removing the stock head
4) Take note of the retention bolt in both the replacement head and your stock head. You will need to remove both of these bolts. This bolt is about 35mm from the top of the head. It will be tight, and it has a nut. I used small pliers to hold the nut and an allen wrench to remove the bolt. The white substance on the end is loctite, that’s why it is a bit hard to remove. A good general rule here is to keep the stock parts separate from the upgrade parts, so you know which go to which. 5) I also loosened the screws around the shaft brace (at the top of the frame where the shaft runs through it). To do this, loosen the 4 bolts (on each side) of the frame. 6) You do not need to loosen the collar around the stock shaft if you are going to re-use it. I strongly recommend you do check the shaft to see if it is straight by rolling it on a smooth flat surface (will save you work later). 7) Remove the swash pitch ball (with the longer screw) from the front of your swash. This is important to note for later. Set aside the stock pitch ball, so you don’t try to use it for the upgrade but you can keep it as a spare. 8) Now you can remove the linkages (clevis) from the swashplate in order to be able to remove the head. 9) You have replacement parts for: the shaft screw at the top of the new rotor head, main rotor blade bolts and nuts, and the new pitch ball with the extension on it), clevis parts. a. Optional, you can remove the plastic vertical fin support for your pitch swash (helps to get it out of the way), keep it you will need it and the mounting screws. 10) Turn the shaft (holding the head still) or turn the drive gear while holding the head still. If it rotates, then you can pull it out of the head. If not, then check to see what is binding it. There is only one retention screw at the top of the head, make sure it is removed. 11) Pull up on the stock plastic head from the shaft, at this point the head should be free to be removed from the heli. a. I strongly recomend you check the shaft is straight before resuing it (will save you work later). Shaft Replacement - Separation from drive gear
12) If you are re-using your shaft and have not removed it, you can skip to Installing the upgrade. At least checking that your drive shaft is true is strongly recomended 13) Remove the retaining bolt from the bottom of the drive gear (the big blue gear) that is attached to the drive shaft. The shaft can now be removed to be checked or replaced. Tip – There is a brass colored ring that rests on top of the blue gear, keep track of it!
- Reattaching drive gear
14) If you removed the retention collar to check the shaft, note the notch in the shaft used to hold the collar in place vertically on the shaft. Position the collar over that notch with the beviled edge of the collar making contact to the bearing ontop of the heli frame. Tighten the collar loosely for now. Note - When inserting the shaft onto the drive gear (note the notch position on the shaft for the retention collar, make sure you account for where it is going to end up (just above the top of the heli frame). Tip - chances are if you look through the bottom bolt hole of the gear for the drive shaft, you won't see light. There is a metal sleeve that needs to be aligned. Pull apart the upper and lower gears, they should separate easily. Gently take your needle nose pliars and re-align the sleeve to the hole. Then put the gears back together. If it keeps moving on you, try inserring the retention bolt (or toothpick) now to hold the gear pieces in place. Then reinsert the gear back into the heli frame. Remove the bolt (or toothpick) after you have lined up the shaft to go back into the gear, then remove the bolt (see below). Tip – When reinserting the shaft try to eyeball the alignment of the holes in the shaft to the holes in the gear you want to put the retaining bolt through. To make fine corrections change the alignment so that you can see light through the shaft and gear hole. Avoid twisting the shaft in the gear if you can, or unless you just need to make a very small correction. A toothpick or small piece of wire or rod can help in completing this alignment. a. Double check that the shaft is oriented properly (the beveled side of the collar faces down). 15) Reconnect the drive gear to the shaft by using either your stock or replacement bolt. This also has loctite on it, so you will need to apply it. Tip – apply the loctite to the very end of the bolt, before sliding the bolt through the gear hole and shaft. The nut is attached to the gear, so this is the only way to apply the loctite. a. Thread the bolt through and tighten, you want it snug but don’t be over zealous, you are driving into a plastic gear with a nut, not just metal to metal. b. When tightening the retention collar, gently squeeze together the bottom of the drive gear, and the retention collar, then tighten the collar. This helps eliminate any slop betwen them. c. Now your ready for the CNC head!
Installing the upgrade- Head
16) To begin this set of steps, your shaft and retention collar should be installed, with the shaft ready to receive the upgraded CNC head. 17) Per step 1, at the beginning, if you have not removed the shaft in the replacement CNC head, do so now. 18) Slide the new CNC head down onto the shaft. 19) Now you can turn the shaft in the head to line up the set bolt you removed in step one above. 20) Install the replacement or stock bolt and nut (either will work). a. In doing this step, don't apply loctite to the end of the bolt after you have threaded it through the hole. Do that after you have set up the swash plate! b. Then apply the nut by holding it up against the end of the bolt you applied the loctite to (the end sticking out sideways with the threads). c. Hold the nut in place with your finger, and screw in the bolt into the nut till it begins to hold the nut securely d. Then use pliers to hold the nut while you tighten the bolt from the other end. 21) This needs to be tight, but don’t strip the threads.
- Swashplate
22) Select a ball on the swash plate to remove, and use a Phillips to remove it 23) Now from your replacement parts, locate the elongated ball used for your pitch, like the one you previously removed, only use the replacement one. Make sure the ball is closest to the swash and the elongated part faces the front of the heli. a. Caution – you can use the stock bolt and ball you removed earlier, but you will end up enlarging the hole for this ball in the swash arm, and it is a VERY tight fit. Better to use the replacement one provided with the upgrade. On mine, there was a difference of about .125 mm between them, the stock being larger. 24) Reconnect the pitch servo to the swash plate ball 25) Slide the pitch servo arm guide (the piece that sticks up from the heli frame like a hoop) onto the end of the pitch ball extension. It should clip on with a little pressure. Start at a 45 degree angle and push it on. a. Tip – the flat part of the arm guide faces the swashplate. 26) Reconnect the arm guide now to the top of the heli frame (using the holes closest to the swashplate on either side of the frame (where it was originally connected). 27) Now you can reconnect the other linkages for the ailerons and elevator. a. If these do not line up properly, then you have missed a step in how the swashplate is set up. Review those steps. b. Your servos should be “roughly” centered and the swashplate should be “roughly” level, you may need to check with your transmitter if your servo arms are not in “neutral” or at zero throw.
- Flybar
28) Connecting the flybar to the flybar seesaw holder that the main shaft runs through a. When I did this my flybar holder was not secured yet to the flybar seesaw, so I lined up the pieces and gently squeezed them together. b. Don't forget to tighten the allen screws that hold the collar in place and the four bolts on the frame where the bearing housings are Tip - Use both of your .5mm allen wrenches to tighten the bolts on the frame for the bearings. I noticed this helps in getting them secure.
- Alignment check
29) Now you can check to see that what you have done is correct a. Make sure your flybar holder, and main blades are level, zero pitch on the main blades, flybar holder horizontal (flat). b. All of your ball linkages should be vertical (straight up and down) attached to the swashplate, servo arms should be perpendicular (90 degrees, forming a L from the ball on the servo arm to the ball on the swashplate. c. Make any corrections necessary before connecting the battery for the transmitter test.
- Transmitter check for response & alignment trim
30) With the throttle all the way down, turn on the Transmitter 31) Now connect the battery to the BR Tip – you might want to use the kill switch on the upper right hand side of the stock Exceed radio if you left it in default mode, flip that switch up. 32) Move the elevator, rudder stick as if you were doing a pre-flight test a. With the heli facing away from you, rotate the head so the flybar holder in perpendicular to the nose of the heli, main blade holders in line with the body of the heli b. R (right) stick to 3 o’clock (OC) dips swash & main rotor mounts to left, R stick to 9 OC dips swash & main rotor mounts to right c. R stick to 12 OC dips swash & flybar holder forward, R stick to 6 OC dips swash & flybar holder backward d. Slowly throttle up with L (left) stick (kill switch up towards you), the swashplate moves up, and the main rotor pitch changes as you throttle up, the swashplate moves down as you throttle down, and the pitch should flatten out (go from positive to negative or almost flat). This will depend a lot on how your set up. e. Manually spin the head, ensure it moves freely and that your tail rotor also moves with the head. f. With your L stick at 50% throttle and centered, visually check your swash again. Reminder - all of your ball linkages should be vertical (straight up and down) attached to the swashplate, servo arms should be perpendicular (90 degrees, forming a L from the ball on the servo arm to the ball on the swashplate.
- Spinning up the head under power
a. With the throttle all the way down, flip the kill switch (upper right switch on transmitter) down (away from you). b. Slowly ease up to ¼ throttle to test to make sure that the head spins under power. i Do not over rev the head in that it needs the weight of the flybar and main blades to help stabilize it. ii Verify the head turns and that the main rotor blade mounts are tracking true. The flybar holder appears to need the weight of the flybar and paddles to stabilize it, my flybar holder wobbles a bit with the flybar and paddles missing. iii Throttle down, disconnect battery, turn off transmitter iv. If you notice any wobbling other than the flybar holder, check to make sure you have tightened up the frame bolts, and you have no loose balls or linkage issues.
- Reconnect blades and paddles
33) Attach flybar, weights and paddles a. For plastic paddles use some CA glue to secure them once you have leveled them. Make sure the flybar is centered beofore you tighten down the flybar allen bolts that hold it. Remeber they face opposite directions! 34) Attach main rotor blades, make sure you install them in the proper direction with the leading edge matching the rotoation of the flybar paddles. 35) That completes the CNC head installation. 36) Here is a excellent set up video for a 450 that walks you through setting up your swash, flybar paddles, and main blade pitch. http://www.moretraction.com/helis/setup%20videos.htm
Happy flying all, Tristar
Last edited by TRISTAR7737 on Wed May 27, 2009 3:47 am; edited 18 times in total (Reason for editing : edited for flybar, checking shaft, and positioning of blades) | |
|  | | P3tras

 | Subject: Re: Blue Ray 450se Upgrades & Tips Wed May 13, 2009 8:37 am | |
| Really good guide  | |
|  | | Donnie D

 | Subject: Re: Blue Ray 450se Upgrades & Tips Wed May 13, 2009 8:40 am | |
| Looks like a good sticky to me. Donnie D  | |
|  | | TRISTAR7737
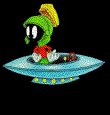
 | Subject: Blue Ray 450''''s kissing cousin EXI Squadron 450 Tue May 19, 2009 12:56 pm | |
|
Last edited by TRISTAR7737 on Tue May 19, 2009 2:52 pm; edited 1 time in total | |
|  | | TRISTAR7737
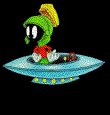
 | Subject: Plastic vs. Carbon Fiber Flybar Paddles Tue May 19, 2009 1:14 pm | |
| I've had a lot of difficulty keeping my plastic flybar paddles aligned, even after securing them with CA glue. I higly recommend the carbon fiber paddles which have retention bolts to secure them to the flybar. 18H-MM0044 at http://www.xheli.com/blueray450.htmlMay not seem that big a deal until one of your plastic ones comes off like one of mine did. If your stuck with the plastic for now, run your CA along the threaded part of the flybar, then screw in the plastic paddle. Tristar | |
|  | | Nuttcaze Admin

 | Subject: Re: Blue Ray 450se Upgrades & Tips Wed May 20, 2009 2:42 pm | |
| I've had the same problem, I switched to align t-rex plastic paddles to solve the prob but I sure would like some carbon fiber ones.  | |
|  | | TRISTAR7737
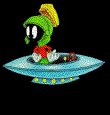
 | Subject: Programing your Volcano ESC Wed May 20, 2009 9:47 pm | |
| How to program your Volcano ESC on your BlueRay After replacing my stock reciever, my throttle was spooling up the heli when set to zero. This link is a great resource on how to "program" the throttle in the ESC. http://www.mycoolheli.com/volcanoesc.htmlcourtsey of dditch66 on RCdiscuss forum. | |
|  | | TRISTAR7737
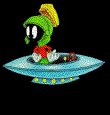
 | Subject: Blue Ray drive gear collar bushing Sat May 23, 2009 1:32 am | |
| Fyi for an Align part # for the bushing for the top of the BR drive gear, comes 2 to a pack.
AGNH1268 One way bearing shaft collar 1.6mm thick (2) | |
|  | | TRISTAR7737
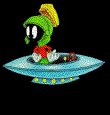
 | Subject: CNC Metal tail upgrade for Blue Ray 450se 18H-M0014 Mon May 25, 2009 3:16 pm | |
| Tips for installing the CNC metal complete tail set upgrade 18H-M0014
Preparation: This assumes you have removed the tail unit you are replacing, and removed the retaining bolts that hold the two halves of the CNC tail unit (http://www.xheli.com/18h-mm0010.html) together, leaving you with 2 halves. The replacement comes with 2 replacemnt belts, control rod linkage for the ball, ball and retention screw (remember the ball faces up towards the boom when you put int on your control arm). If you previously removed the 2 linkage guides and vertical stabilizer, these go back before you replace the tail unit.
Separating the tail unit: Be prepared for the braces and screws to fall out when you separate the two halves, the screws are all that hold the tubular braces in place. To help gain access to the screws, remove the control arm from the CNC tail assembly. Caution: keep track of the tiny brass washer between the control arm and the metal extension it is attached to. I can be helpful to position the heli on it’s right side (tail rotor facing down), to help keep track of the parts as the halves disconnect.
Securing to boom: When mounting the tail unit to the boom, use one of the supplied CNC tail unit screws that you will mount the vertical stabilizer ( the one that takes 3 screws in a row) and line it up the hole in the boom to install the middle screw. This will let you align the tail unit before attaching the vertical stabilizer later. Loosening the 4 retaining screws on the rear of the heli frame will let you slide the boom forward, making it easier to handle the drive belt. You can either remove the tail braces, or loosen the vertical fin on the tail boom. Tip: If the frame screws just spin, use two allen wrenches (on each side of the frame) and tighten the screw you want to loosen. You may need to just slightly tighten both screws. This will release the screw enabling you to loosen it.
Checking your belt You need a 90 degree twist in your belt to connect the tail rotor shaft gear. If you carefully removed your tail unit, the belt "should" retain its alignment. Otherwise you need to position the belt to align with the gear on the tail rotor shaft your installing. Caution: I strongly recommend you check your belt orientation before joining the halves back together, see tip below.
Tip: Pulling on the top of the belt (sticking out of the boom) the main blades must move clockwise for your tail rotor to turn counterclockwise (as viewed with the nose of heli facing right). If in doubt check your pictures, the leading edge (blunt edge) of the tail rotor blades face the back of the heli, not the nose.
Joining the halves:
Tip: use some tack or silly putty (what you can get at the stationary section to temporarily put up papers) to hold the screws and the brace parts in place to make joining the two halves of the CNC tail unit together, see picture. Work in a cool area, don’t let the tac get warm, it will become too sticky and residue will cling go parts. The tack helps in keeping the parts aligned. Keep the tack away from the surfaces you are joining. It may be easier to lay the heli on its right side, positioning the half with the tail rotor on the boom, screws facing up, and then aligning the left plate side of the tail rotor on top. Holding the right half in place, pull on the tail boom to snug up the belt after you place it in the tail unit.
The metal tension wheel pushes down on the belt, make sure it is exposed, facing up. Tip: Once you join the halves, press together the end of the tail unit closest to the boom when reinserting the bolts to hold the tail unit together. Remove the tack or putty from a screw furthest from the heli or boom, and loosely tighten, repeat for a screw towards the boom. Then remove the putty or tack, loosely tightening the bolts as you go. Now, test if belt is properly engaged. The tail rotor turns with the main blades. You may need to pull the boom out from the heli (gently) to get it taunt to test this. If turning main blades clockwise causes the tail rotors to move counter clockwise, you can proceed. Otherwise go to checking your belt above. Tip: Don’t over tighten the bolt for the silver tension wheel! Ensure this wheel is spinning freely. The belt goes around the tail rotor gear, under the silver tracking wheel and inside all 3 silver tail assembly spacers.
Vertical fin & control arm Now that you have applied blue locktite, and tightened the screws holding the halves together , you can reattach the vertical stabilizer. Suggestion: use stock carbon washers from other parts on these bolts since the replacement CNC tail unit does not provide any. When reattaching the control arm, slip the ball connected to the tail rotor shaft first, then screw in the bolt into the sliver metal arm (don’t forget the tiny brass washer). Reattach the control rod, ensure it and the tail control arm move freely. Tighten or reattach the boom brace / horizontal fin.
Blades: Attach your blades with the leading edge facing counter clockwise, front of heli facing left. Check to see if the pitch of the tail rotors changes as you move the control arm. Left stick at 9 O’clock should push the tail rotor blades to the right, and increase their positive pitch (pushes nose left, tail right), Left stick at 3 O’clock pushes nose right, tail left (increases negative pitch). Left stick centered should have a slight pitch (as if you moved your left stick slightly to the left)
May your upgrades serve you well, Tristar
For more info:
From dditch66 see Blue Ray tail servo / gyro install at http://www.mycoolheli.com/tailservosetup.htmlFrom Skidsup see DX7 config for a 450 belt heli at http://www.crackroll.com/forums/showthread.php?p=11687
Last edited by TRISTAR7737 on Wed May 27, 2009 4:02 am; edited 5 times in total (Reason for editing : Made correction to checking belt for proper tail rotation, view perspective) | |
|  | | TRISTAR7737
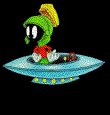
 | Subject: Update on CNC Heads on Parts Replacement Page Fri May 29, 2009 1:48 pm | |
| Here is data from Andy on RC Disucss on the CNC Head Upgrades
18H-MM0029 is for blue ray 450
18H-M0099 is for legend 450 excel style
18H-M0629 is for legend
18H-M0699 is for blue ray 450 excel style
Good News!, MM0029 now has a 115mm shaft!!! I got a backup (ordered in May '09) I installed it to check. These newer kits have a stock shaft FITS!
Happy upgrading.
Last edited by TRISTAR7737 on Sun May 31, 2009 8:49 pm; edited 2 times in total (Reason for editing : Added test results of new repacement CNC heaad assembly) | |
|  | | TRISTAR7737
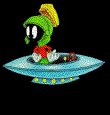
 | Subject: Recommendation for replacing your tail drive gear Thu Jun 11, 2009 3:20 pm | |
| I've read on RC Disucss that the stock and repacement tail gear bearing set (the gear comes with the bearings and housing for it). 18H-PP0028 (plastic) and 18H-MM0028 (cnc) have a tendency to slip after time. The plastic head that drives the tail belt off of the main gear slips, as mine did with some abuse after some weed whacking Try the T-Rex replacement instead. It has a metal head that drives the tail belt that you attach, so you can use ca or an adhesive to keep it from spinning. http://www.t-rex-parts.com/T-Rex_450_Parts/c23/p1674/T-Rex_450V2_Metal_Tail_Drive_Gear_Assembly/product_info.html After installing this, I also had more clearance for my servo, the stock part was actually making contact with the bottom of one of my servos. May your tail gear drive never spin! | |
|  | | meanbaby

 | Subject: Re: Blue Ray 450se Upgrades & Tips Thu Jun 11, 2009 3:34 pm | |
| Great write up Tristar, this can also applies to other helis more or less also!
-pete | |
|  | | Sponsored content
 | Subject: Re: Blue Ray 450se Upgrades & Tips  | |
| |
|  | | | Blue Ray 450se Upgrades & Tips | |
|
Similar topics |  |
|
| Permissions in this forum: | You cannot reply to topics in this forum
| |
| |
| |
|